Surface finishing of metals is essential for enhancing appearance, durability, and performance.
Consider the smartphone you use every day. The metal casing, often made from aluminum, must be durable and visually appealing. Surface finishing techniques like anodizing creates a protective oxide layer that resists scratches and corrosion while allowing for vibrant colors, giving your smartphone a sleek and attractive finish.
Metal surface finishing is used in many applications, from the car you drive to surgical instruments.
You might be asking, what are the various metal surface finishing techniques available? How do you determine which method is most suitable for your project? What benefits do each of these techniques offer?
This post will delve into the nine most crucial surface finishing processes. By the end, you will clearly understand the standard techniques applied to metal surfaces, learn to identify the methods used in the metals you encounter, and feel more confident in choosing the proper metal surface treatment for your project.
Electroplating
Metal plating is the process of applying a thin layer of other metals such as chromium, nickel, and zinc over the surface of base metal to enhance chemical resistance, durability, corrosion resistance and surface friction of base metals as per requirement.
There are two major types of metal plating. We will start with electroplating.
Electroplating involves a metal deposition process where one metal is deposited onto the surface of another base metal. The metals used for deposition in this process are known as plating metals. Copper, nickel, chromium, zinc, silver, and gold are commonly used plating metals in electroplating.
The process uses components in a bath containing metal ions for coating. A direct current is applied to the metal to ensure proper ions deposition on the surface, forming new layers on the base metal. Imagine a bath with a copper sulfate (CuSO4) solution and a device that supplies electric current. When the switch is turned on, the cathode bar holds the metal piece and gets a negative charge. This negative charge attracts positively charged copper ions (Cu2+), which then stick to the surface of the metal piece, creating a new layer of copper.
You might wonder how the copper ions are kept available for the process to continue. The sulfate ions (SO42-) in the solution react with the copper anodes to form new copper sulfate, thus maintaining the solution’s composition.
The following video illustrates electroplating and how it works.
Electroplating is used in various industries. It enhances the durability and corrosion resistance of parts like bumpers and wheel rims in automotive. In electronics, it coats connectors and circuit boards with metals to improve conductivity and prevent oxidation. In the industry of jewelry, it gives inexpensive metals a luxurious finish and increases their longevity by coating them with precious metals.
Electroless plating
Electroless plating is another type of metal plating.
This process is also known as autocatalytic plating, which does not require any external power. Instead, metal components are deposited in solutions of nickel or copper, which starts the process by breaking metal ions for the formation of chemical bonds.
If you are looking for surface finish techniques that protect metal surfaces from corrosion, wear, and abrasion, electroless plating is an outstanding available alternative. Electroless plating is a crucial metal finishing process that offers unique advantages for specific applications.
The video provides a clear explanation of the process.
Preparing the surface for the electroless plating is crucial for its success. The bonding issues can occur on uneven, rough surfaces having burrs and surface defects can make the situation worse for electroless plating.
Hot Dipped Galvanizing
The hot dipped galvanizing process, a widely used metal finishing technique, starts with the cleaning of steel and dipping it in the molten zinc bath at 450◦C to obtain coating on the surface of the steel sheet. This product is highly suitable for extremely harsh environments and protects against corrosion.
As shown in the process flow diagram, the material being galvanized is rinsed with water and pickled for cleaning purposes to ensure a neat clean surface before immersing it in a molten zinc tank for proper chemical bonding and smooth surface.

Galvanizing is particularly suitable for outdoor structures like bridges, guardrails, fences, and automotive parts such as chassis and frames. In construction, galvanized steel is used for roofing, wall panels, and beams. Due to its protective zinc coating, agricultural equipment, marine structures, HVAC systems, public infrastructure, and pipelines also benefit from galvanizing.
Electropolishing
Electropolishing, also known as electrolytic or anodic polishing, is a process in which the surface roughness of the metal components is reduced by up to 50% to give them a smooth aesthetic appearance. It uses an electric current in a unique solution to remove tiny bits of metal from the surface. The process is the opposite of electroplating, which adds metal to the surface.

The five most important factors to consider when removing material from the surface of the metal in the electropolishing process are the electrolyte temperature, chemical composition of the electrolyte, time duration of exposure to electric current, composition of the metal undergoing electropolishing, and current density used in the process.
With electropolishing, the metal ions are removed, resulting in a smoother and more attractive finish. Figure 3 shows that highly concentrated current, along with electrolytes, eliminates defects from the surface and results in a smoother surface with an aesthetic appearance.

Electropolishing finishes surgical instruments and implants in the medical and pharmaceutical fields, reducing contamination risk. The food and beverage industry benefits from its smooth, easy-to-clean surfaces that minimize bacterial contamination. In semiconductor and electronics manufacturing, electropolishing ensures high precision and cleanliness. Marine and chemical processing industries rely on it for improved corrosion resistance and reduced surface roughness. Lastly, architectural and decorative applications employ electropolishing to achieve high-gloss, reflective finishes on metals like stainless steel.
Metal Grinding
Grinding machines have been used in the manufacturing process to smooth the surface of metal by using abrasive materials. It is one of the last stages in the machining process that reduces surface roughness and imperfections of metallic components, as shown in Figure 4.
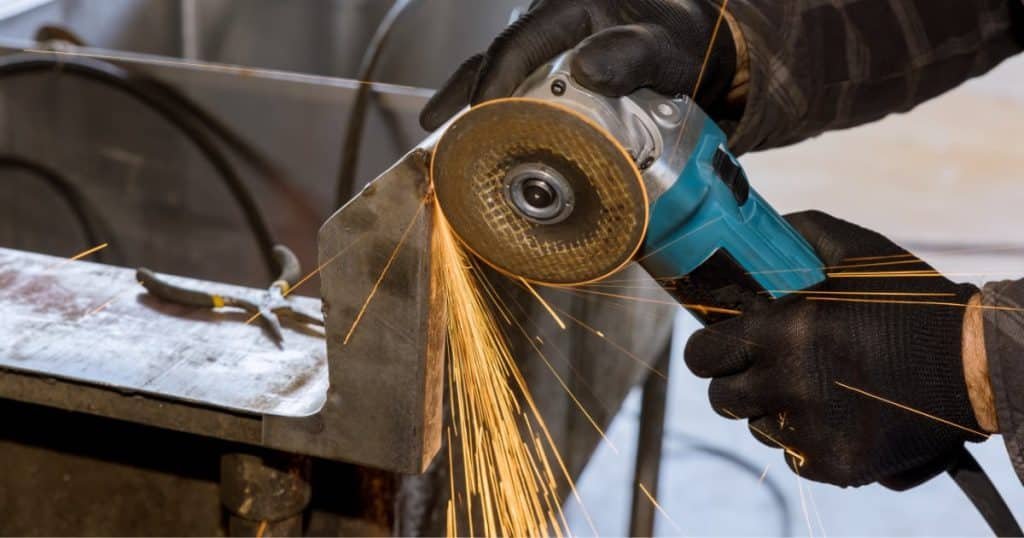
Grinding is commonly used in the automotive industry to smooth out engine parts. It’s also essential for turbine blades in aerospace and precision tools and dies in manufacturing. This process can also be employed in the construction industry to finish metal beams and frames.
Painting
Painting is one of the subcategories of coating and is the least expensive. As one of the metal finishing techniques, commercial paints are used to give metals a visually appealing look, but some paints are not only about looks. Sometimes, paints are used to prevent corrosion.
When selecting a surface finish for a metal project, it might seem straightforward to paint any color over it. However, it is surprisingly intricate to see how different paints affect metallic bodies. Some paints are specially designed for protection against rust and are incredibly durable.
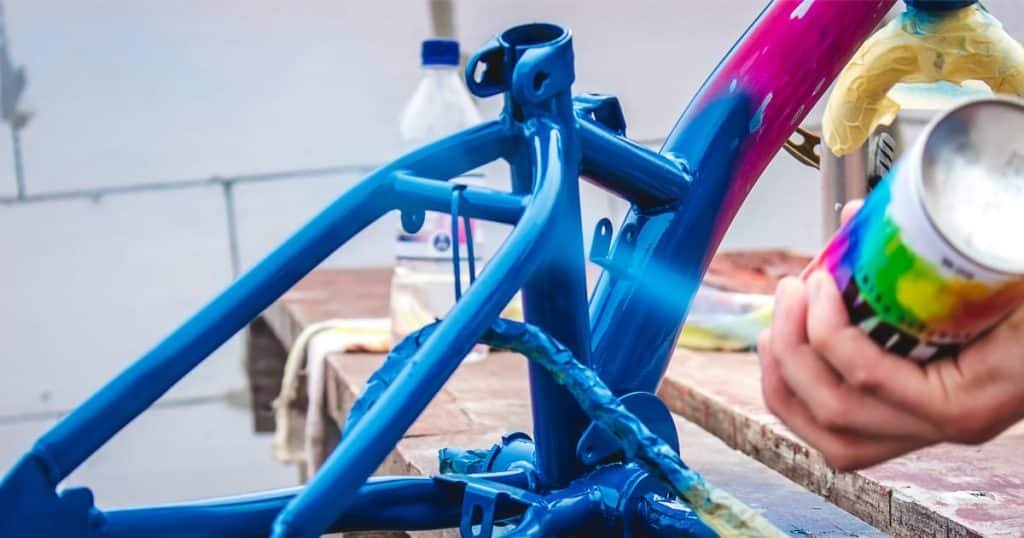
So, if you are looking for a cheap and durable option for surface finishing, whether a garden bench or metallic project, try to research yourself, find out the need and role of painting in your project, and select the most appropriate one.
Powder Coating
The modern type of painting is a game-changer metal finishing technique. It’s a process that uses an electrostatic charge to attach powder particles to metals.
This is not just a paint job, but it is super-efficient and high technology.
The process starts when the charged particles stick evenly on the surface of the metal, where they get treated with ultraviolet rays or heat, creating a smooth and durable finish. It is like giving your metal parts a high-quality surface finish.
This powder coating involves three primary stages: part-preparation or pre-treatment followed by powder application and curing.

You can find powder coated metals in many places. If you have outdoor furniture, you might appreciate its durability against the elements. In household appliances, mailboxes, metal cabinets, powder coating provides a long-lasting, attractive finish.
Abrasive Blasting
Abrasive blasting is a surface finishing technique used by anyone looking for a consistent matte texture on their metal products. It is cost-effective as it combines surface finishing and cleaning in one swift operation.
During the blasting process, high-pressure abrasive material hits the surface of the metal which not only modifies texture but also removes debris and imperfections to produce a smooth surface of the final product.
Blasting is a simple process, and you can classify it into three major types: shot blasting, sandblasting, and blower blasting.

Blasting can prepare metal surfaces for painting, clean industrial equipment, and remove old paint and rust from car bodies.
Anodizing
Anodizing is an electrochemical metal finishing technique that creates a durable, strong, and corrosion-resistant anodic oxide surface finish for metal components. You can select it to give your metal parts a stylish and attractive coating. The figure below is an example of anodized aluminum.
This works like when you soak an aluminum part in an electrolyte bath and pass an electric current through it. The aluminum part serving as an anode(positive electrode) and an inert cathode(negative electrode) are in the anodizing tank. The oxygen ions released from the electrolyte combine with positively charged aluminum ions to form an aluminum oxide on the surface of the aluminum part.
This surface finish technique is a highly controlled oxidation of metal substrate. It is mainly used for finishing aluminum parts but is also effective for non-ferrous metals like titanium and magnesium.
The video below provides detailed information if you want to learn more about anodizing and how it works.
Anodized aluminum protects your satellites and is used in one of the tallest buildings on earth, the Willis Tower in Chicago, Illinois. It is also used in consumer electronics, cookware, and architectural elements.
Comparison Chart of Metal Surface Finish Techniques
Different types of metal require specific finishing techniques to optimize performance and appearance. The above introduces the nine essential metal surface finish methods. Here, I have simplified it for you with a table showing the types of surface finishes for different applications and their benefits and considerations.
Type of surface finish | Applications | Benefits | Considerations |
---|---|---|---|
Electroplating | Jewelry, electronic components, automotive parts | Corrosion resistance and aesthetic appearance | Precise control of process is needed. |
Electroless plating | Electronic parts | Excellent for complex shapes | Slow process and expensive |
Galvanizing | Automobile frames, outdoor structures | Durable and corrosion resistance | Mechanical properties are affected. |
Electropolishing | electronics and automotive parts | Smooth finish | Labor needed and is expensive |
Metal grinding | Steel sheets, automotive parts, aerospace industries | Removes material and provide uniform texture | Can generate heat require trained professional |
Painting | General fabrications and automotive parts | Cost-effective, adds colors, and effective for corrosion resistant | Paint contains solvents and volatile organic compounds, harmful if inhaled and are flammable. |
Powder coating | Outdoor furniture, metal cabinets, industrial equipment frames | Durable, high quality and fast process for industrial or large-scale applications | Requires UV rays or heat. Higher initial investment in equipment. |
Blasting | Metal parts | Smooth finish and cleans surface properly | Requires proper labor |
Anodizing | Building structures and electronics | Corrosion resistance and aesthetic appearance | Limited to aluminum, its alloys and a few metals |
Choosing a suitable surface finishing technique is essential for the durability and appearance of final products. These treatments are very beneficial if you are looking for corrosion resistance, aesthetic appeal, improved performance, and longevity.